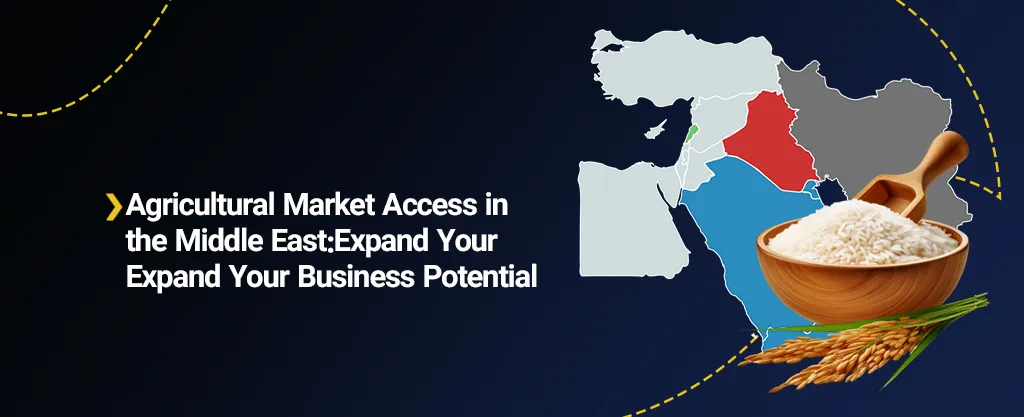
The Middle East and North Africa (MENA) region has more than 578 million inhabitants and relies heavily on foods that are not produced within the area.
Applying efficient plans while purchasing can significantly reduce the risks of poor quality, resulting in satisfied customers and improved operations. This article examines holistic means that sellers can employ to ensure product quality while acquiring products directly from manufacturers or suppliers.
Making sure products are of quality from the get-go isn't just a safety precaution—it's an important strategy for retailers who want to establish trust, minimize returns, and uphold a positive brand reputation. When companies buy products straight from suppliers or manufacturers, they can check standards, review materials, and outline exact specifications before products hit retail shelves. Here we will explore why source quality control is so important and how traders can utilize intelligent and practical approaches to reduce risk and enhance customer satisfaction.
Before engaging in business with a supplier, it's important to evaluate their capacity to supply to your level of quality. This ought to include:
Site visits can be used to gain firsthand information about the operations and quality control of the supplier.
Defining specific quality needs is crucial. Give comprehensive product specifications that outline materials, dimensions, performance standards, and tolerance levels that are acceptable. Good documentation promotes a common understanding of the required quality by both parties, diminishing the prospects of misunderstandings.
Include some quality-related terms in contracts, e.g.:
Well-written contracts are legal protections and establish clear expectations for quality assurance.
Ordering sample products before mass production enables quality testing against standards. This isolates and addresses potential problems early on, making it possible to adjust materials or processes of manufacture to guarantee the desired end product.
Develop a plan that describes the quality control measures during the production process, including:
Periodic checks ensure that quality is consistent and faulty goods do not reach the customers.
Hiring independent testing organizations to confirm product quality provides an additional guarantee. Third-party certification can ensure adherence to industry standards and government regulations, providing greater credibility and consumer confidence.
Creating open and frequent channels of communication with suppliers enables the quick resolution of quality-related problems. Strong relationships foster cooperation in solving problems and making improvements.
Establish a system for monitoring supplier performance with key performance indicators (KPIs) like defect rate, on-time delivery, and responsiveness. Ongoing monitoring allows trends and issues to be identified and addressed through proactive quality management.
9. Invest in Supplier Development: Collaborate with suppliers to enhance their quality management capabilities by training, sharing best practices, and providing resources. Investment in supplier development can lead to long-term supply chain efficiency and product quality gains.
Depending on one supplier is always a gamble. Having diversified suppliers reduces risks linked to quality problems, supply breakdowns, or capacity limitations. Having alternative sources guarantees continuity and upholds quality levels.
Utilization of quality management software can automate processes such as inspection tracking, document control, and analysis of data. Technology enhances efficiency and provides real-time quality performance feedback.
Arrange regular audits of the supplier facilities and quality systems to monitor continued compliance with the agreed standards. Regular audits identify areas for improvement and emphasize the priority of quality in the supplier relationship.
Having good quality products when buying directly from manufacturers is important for sellers who want to retain customers and protect their brand reputation. Following good strategies can help in achieving consistent product quality. Here are five main ways:
Before entering into a partnership, scrutinize potential suppliers thoroughly. This involves looking at how they produce goods, how they manage quality, if they adhere to industry standards, and if they are financially capable. Going to their sites and asking for references from previous customers can give valuable insight into their quality processes and reliability.
Define and notify your suppliers of specific quality standards. Providing product specifications, tolerable limits, and desired performance criteria in writing ensures that the two are on the same page. Recording these specifications in a contract can be a point of reference and prevent misunderstanding. 3. Carrying Out Rigorous Inspection Processes Use systematic inspection on different levels of manufacturing the product. This entails inspection before manufacturing, during processing, and before shipping. Employing external quality control companies can provide unbiased testing and verify that products meet the agreed-upon standards before shipment.
Depending on one supplier is always a gamble. Having diversified suppliers reduces risks linked to quality problems, supply breakdowns, or capacity limitations. Having alternative sources guarantees continuity and upholds quality levels.
Utilization of quality management software can automate processes such as inspection tracking, document control, and analysis of data. Technology enhances efficiency and provides real-time quality performance feedback.
Arrange regular audits of the supplier facilities and quality systems to monitor continued compliance with the agreed standards. Regular audits identify areas for improvement and emphasize the priority of quality in the supplier relationship.
Having good quality products when buying directly from manufacturers is important for sellers who want to retain customers and protect their brand reputation. Following good strategies can help in achieving consistent product quality. Here are five main ways:
Before entering into a partnership, scrutinize potential suppliers thoroughly. This involves looking at how they produce goods, how they manage quality, if they adhere to industry standards, and if they are financially capable. Going to their sites and asking for references from previous customers can give valuable insight into their quality processes and reliability.
Define and notify your suppliers of specific quality standards. Providing product specifications, tolerable limits, and desired performance criteria in writing ensures that the two are on the same page. Recording these specifications in a contract can be a point of reference and prevent misunderstanding.
Carrying Out Rigorous Inspection Processes Use systematic inspection on different levels of manufacturing the product. This entails inspection before manufacturing, during processing, and before shipping. Employing external quality control companies can provide unbiased testing and verify that products meet the agreed-upon standards before shipment.
Carry out regular inspections at different phases of manufacturing products. This includes inspection before production, in the course of production, and before shipping. Outsourcing quality control companies can provide independent evaluation and assurance that products have attained agreed-upon standards before shipping.
Good supplier relationships, built and nurtured through effort, guarantee greater cooperation and coordination. Regular contact, feedback sessions, and joint problem-solving programs can fuel continuous improvement in product quality and faster response service.
Ongoing Performance Monitoring Track and assess the performance of suppliers against key performance indicators (KPIs) like defect rate, on-time delivery, and how quickly they respond to quality problems. A supplier scorecard system will help with monitoring improvement over time and pinpointing areas that need improvement.
With these strategies in your procurement practices, you can drastically improve the quality of your products and gain a more stable supply chain.
Conducting thorough supplier audits guarantees that potential suppliers fulfill your quality requirements and regulatory adherence. Conducting frequent audits can reveal discrepancies and areas for improvement to guarantee a steady alliance.
Utilization of technological innovations, such as quality management systems and real-time monitoring systems, can make the process of quality control easier. These technologies provide data-driven feedback that allows proactive problem-solving and maintenance of product standards.
To ensure quality items when buying at the source, one ought to use several practices. These include carefully screening the suppliers, defining standards clearly, negotiating strict agreements, and policing the process. Using these precautions, retailers will be able to reduce risks, increase customer satisfaction, and develop strong, dependable supply chains.
One service that can help facilitate this process is Momex, a platform that connects businesses with trusted suppliers and offers tools for quality assurance and monitoring, ensuring that products meet the desired standards before reaching customers. Through Momex, retailers can streamline their sourcing process while maintaining the highest quality control.